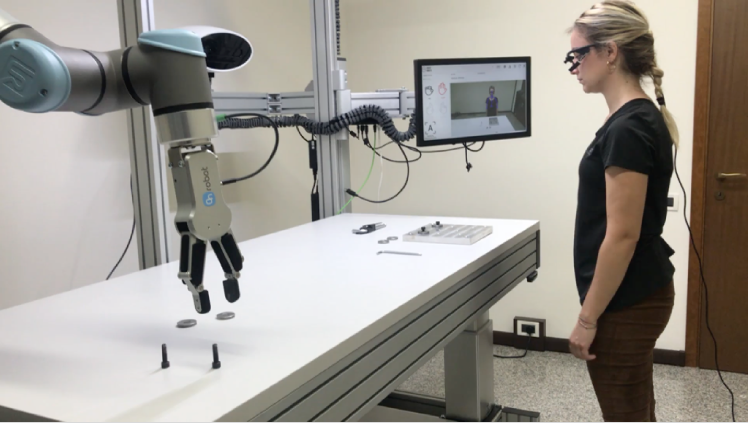
Please enjoy this explanatory article on the research coming from the 2nd Use case of the Coadapt Application Study, which aims at designing developing, and evaluating an Adaptive Assembly Workstation equipped with Collaborative Robotics.
The aim is to create a workstation that meets both the production company duties and the individual worker needs. A highly usable and customizable working tool is expected to produce benefits, especially for senior operators’ (e.g., well-being, reduced stress). The University of Padua and BNP SRL are developing and testing a multi-component adaptive workstation adopting a user-centered design approach. Two prototypes were produced, one installed in a UNIPD laboratory and one installed at the BNP plant. The work on the Adaptive Assembly Workstation and a first experiment were presented at the 19th Eawop Congress in 2019.
“CO-ADAPT: designing an adaptive and accessible 4.0 working environment for the older employees’ needs.” Gamberini, Pluchino, Spagnolli, Orso, & Jacucci. employees’Abstract Book. 19th Eawop Congress (2019)
“Assessing cognitive workload and mental fatigue in the context of human-robot collaboration: a comparison between different metrics.” Pluchino, Mingardi, Barattini, Ragazzon, Pettenon, & Gamberini. Abstract Book. 19th Eawop Congress (2019)
What is an adaptive assembly workstation, and what is a cobot?
An adaptive assembly workstation is a smart manufacturing device capable of implementing a series of adaptations in its structural and operating features. The specific physical, perceptual, and cognitive abilities of the actual operator are taken into account for implementing such real-time adaptations to maximize the technological support. Indeed, the workbench height can be adjusted to match the physical characteristics of the actual operator, or the lighting system can adapt the level of illumination to counteract potential visual impairments (i.e., low vision, contrast perception). The adaptive features also involve modifications in the functioning of the robotic arm. This collaborative robot (cobot) combines the physical and preciseness skills of the traditional industrial robot with several advanced features. Indeed, the cobot is capable of sharing the working tasks with the human operators flexibly and safely (i.e., a set of proximity sensors in the robotic arm ensure the workers’ safety).
Furthermore, it will take charge of the most repetitive tasks that may lead to errors when human operators have to perform them for a prolonged amount of time (i.e., a decrease in attention, vigilance). Finally, the workstation is also equipped with a Smart Robot camera, namely a 3D intelligent vision system. This device is capable of: tracking the human body and movements in real-time to provide a second level of safety (i.e., the cobot stops when the camera detects that it is too close to the operator); augmenting the collaboration with this robotic co-worker; and suppling an additional remote and immediate way of interaction with the cobot (i.e., gestures). Indeed, a set of gestures allows the worker to communicate to the cobot to activate, stop, and change its activity.
Which are the advantages of the introduction of these cutting-edge tools for the workers?
The overall adaptability of such workstations is possible thanks to a human-centric approach in their design and development that carefully considers the operators’ needs alongside the production ones. Workers’ well-being, satisfaction, quality of working life, and productivity will be increased insofar as these working tools aim at decreasing the level of stress and workload, especially for senior operators. Indeed, the non-invasive monitoring of bio-signals (e.g., heart rate, skin conductance) fluctuations and eye behavior (e.g., fixations, blinks), through wearable devices, could be exploited to detect extreme levels of stress and mental workload. It is precisely within this research domain that the use case is currently defining the most suited set of workers’ measures based on which the workstation will implement highly customized adaptations in its operating to support each worker specifically.
Our preliminary investigation, in a laboratory setting, identified the heart rate and several eye-related measures (e.g., fixations, blink, saccades) as the best indicators to distinguish tasks that differ in terms of mental workload and stress. Thus, the combination of multiple psychophysiological measures has proven to be the most reliable solution to adopt. Besides, the continuous monitoring of the operator through wearable sensors is revealed to be necessary for tuning the capability of the workstation to precisely detect situations in which s/he needs support (e.g., cognitive overload, stress).